
THE TRUSTED NAME IN PORTABLE SOLUTIONS SINCE 1985
Our mission at Spot Coolers has been simple: to keep our partners in control of their businesses at all times while we take care of their heating and cooling outages, planned or otherwise.
Good Alone, Better Together
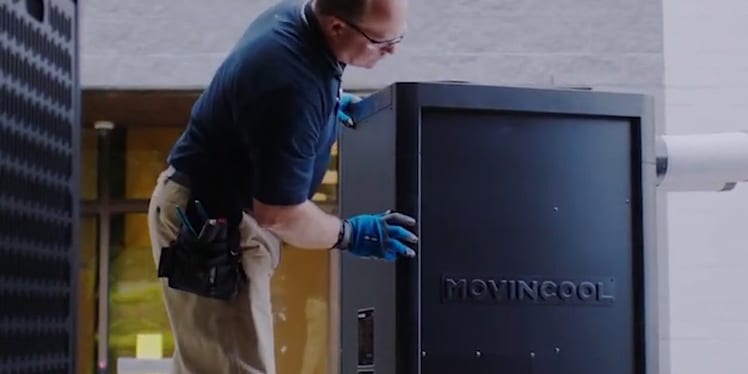
Why Spot Coolers?
Since 1985, Spot Coolers has offered convenience and efficiency through portable HVAC solutions. Our team delivers and installs trusted units such as portable air conditioners, electric heaters, dehumidifiers, and more to answer your needs with 24/7 availability, whether they be emergency rentals or planned maintenance.
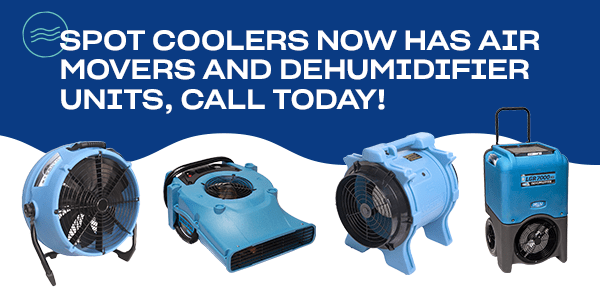
ALREADY KNOW WHAT YOU NEED? REQUEST A QUOTE TODAY!

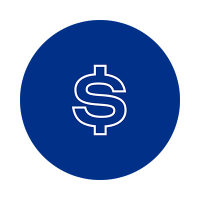
RENT OR BUY
We have portable heating, cooling, dehumidification and air cleaning solutions that fit every budget and project.

RESOURCES
Check out a wide variety of valuable resources for Spot Coolers.

LOCATIONS
Our network of nationwide locations means you’re always covered.